深圳市多賀電氣有限公司成立于2015年12月24日,注冊資金500萬元,總部位于深圳市寶安區沙井街道,專注于電氣控制箱、配電盤、高壓電器元件的研發、生產及銷售,業務覆蓋自動化設備安裝、機電維修及進出口貿易。
?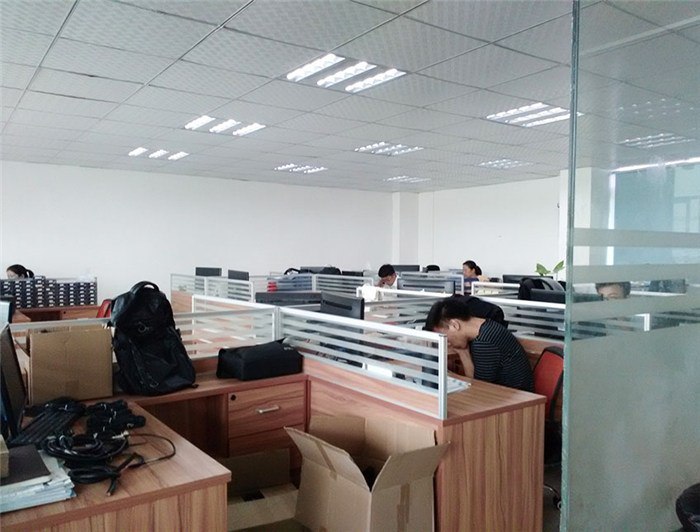
作為國家高新技術企業,多賀電氣產品廣泛應用于新能源、智能電網等領域,但伴隨業務多元化擴張,企業面臨以下核心瓶頸:
-
生產效率滯后:生產周期長,電氣控制箱平均交付周期達18天,客戶訂單準時交付率僅為68%;
-
現場管理粗放:物料堆積占用30%車間面積,員工每日浪費1.5小時翻找零部件;
-
成本管控失衡:線邊庫存積壓超200萬元,設備綜合效率(OEE)僅58%;
-
質量波動頻繁:電路板焊接不良率高達5%,客戶投訴率長期徘徊在10%。
2024年3月,多賀電氣攜手上海博革咨詢集團啟動精益生產變革項目,旨在破解增長困局。
基于“診斷-試點-固化-推廣”四步法,博革為多賀電氣定制三大核心模塊:
1. 價值流重構與柔性生產
-
價值流分析(VSM):識別從訂單接收到產品交付的22個非增值環節,壓縮等待時間47%;
-
單元化產線改造:將配電盤裝配線重組為U型單元,物料搬運距離從150米縮短至40米,生產周期縮短35%;
-
智能物流升級:引入AGV無人車與電子看板系統,實現物料精準齊套配送,送料效率提升55%。
2. 5S與目視化體系落地
-
紅牌作戰:清理冗余設備18臺、呆滯物料12噸,釋放車間面積250㎡;
-
動態管理看板:部署10塊電子看板,實時監控訂單進度、質量SPC數據,計劃排產準確率提升至90%;
-
定置定位管理:采用“形跡管理+色標分區”規范工具與物料存放,員工取料時間從10分鐘降至90秒。
3. 數字化精益融合
-
MES系統集成:打通PLM-ERP數據流,設計變更傳遞時效從72小時壓縮至5小時;
-
ANDON異常響應:設備故障觸發聲光報警,維修人員通過AR眼鏡接收故障診斷方案,異常處理時效提升80%;
-
OEE實時看板:通過IoT傳感器采集設備運行數據,OEE提升至76%。
博革咨詢通過“精益內核+數字化外延”雙引擎,助力多賀電氣從傳統制造向精益智造轉型。這一實踐表明,在電氣裝備行業,精益生產不僅是效率工具,更是企業構建差異化競爭力的戰略支點。